石英坩埚属于石英玻璃制品中的细分产品,具有洁净、同质、耐高温等性能。从物理热学性能上看,它的形变点约为1,100℃左右,软化点为1,730℃,其最高连续使用温度为1,100℃,短时间内可为1,450℃。目前广泛应用于太阳能和半导体领域提炼晶体硅的生产工艺中,是晶体硅生产过程中的消耗品。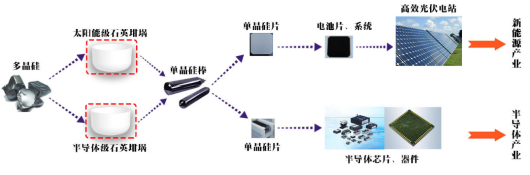
目前,拉单晶的石英坩埚一般是采用电弧法生产,其原理为:将高纯石英粉装入可任意倾动角度的旋转成型模内,利用离心力成型,将已成坩埚形的旋转着的装置移动至电极棒处,然后将电极送电启弧,同时启动真空系统,使其快速熔化成坩埚形状的熔融石英,经冷却后取出,即完成一个石英坩埚的熔制。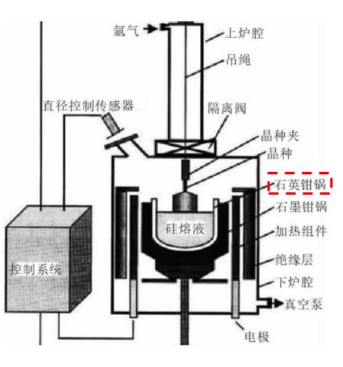
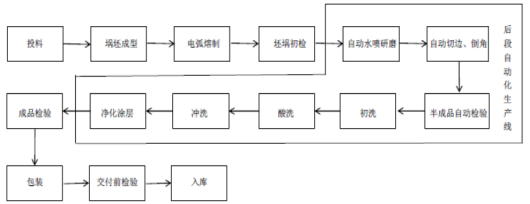
早期的石英坩埚是全透明的结构,这种透明的结构容易导致不均匀的热传输条件,增加晶棒生长的难度,且均匀的结构对高品质的高纯石英砂需求较大,成本较高,因此这种石英坩埚的制备方法基本被淘汰。电弧法制备的石英坩埚为半透明状,有内外两层结构,外层是高气泡密度的区域,称为气泡复合层。气泡复合层受热较均匀,保温效果较好;内层是一层3-5mm的透明层,称为气泡空乏层。气泡空乏层的存在使坩埚与溶液接触区的气泡密度降低,从而改善单晶生长的成功率及晶棒品质。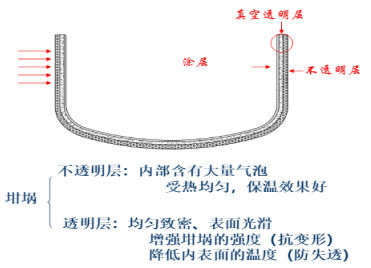
由于下游行业对于石英坩埚的纯度、洁净度、精度具有严格标准,同时大硅片的演进也对坩埚产品提出更高的要求,石英坩埚工艺技术一直向“高纯度、大尺寸、低成本、长寿命”方向发展,行业内企业须要具备较长时间的技术经验积累,逐渐提高产品尺寸、纯度和其他性能指标。
高纯石英砂是石英坩埚核心原材料,其纯度显著影响拉晶效果。拉晶的过程中,石英坩埚内部的羟基、杂质元素和气泡的含量将会影响硅棒的质量和石英坩埚的使用寿命,其中工艺路线能够改善羟基的含量,但杂质与气泡的含量更多依赖于石英砂本身的纯度。羟基(-OH)含量:坩埚中的羟基(-OH)是影响坩埚强度的核心因素,由于羟基的存在,改变了SiO2的键合结构,致使坩埚的耐温性能大幅降低,例如坩埚中的羟基含量超过150ppm,1050摄氏度就会开始软化变形,无法正常使用。坩埚中的羟基含量主要与坩埚制备所选取的工艺路线直接相关,也与环境湿度以及原料选取等有关。杂质含量:石英砂的流体包裹体和晶格杂质中的碱性离子的存在是导致石英坩埚析晶的主要因素,尤其是碱金属离子的存在,将会降低析晶温度200-300℃,导致析晶加速。石英坩埚内壁发生析晶时有可能破坏坩埚内壁原有的涂层,将导致涂层下面的气泡层和熔硅发生反应,造成部分颗粒状氧化硅进入熔硅内,使得正在生长中的晶体结构发生变异而无法正常长晶。此外,析晶将减薄石英坩埚原有的厚度,降低了坩埚的强度,容易引起石英坩埚的变形。因此石英砂纯度对拉晶质量有较大程度的影响。气泡(气体包裹体)含量:气泡(气液包裹体)主要由结晶水和气组成,气的成分主要有CO2、H2O、H2O2、N2、CH4、CO。在坩埚使用过程中,由于与硅液接触的内表面不断向硅液中熔解,并且伴随着透明层中的微气泡不断的长大,靠近最内表面的气泡破裂,伴随着硅液释放石英微颗粒以及微气泡。而这些杂质会以微颗粒以及微气泡的形式伴随着硅液流遍整个硅熔体,直接影响到硅的成晶(整棒率、成晶率、加热时间、直接加工成本等)以及单晶硅的质量(穿孔片、黑芯片等)。目前,通过使用低气泡密度的高纯度石英砂作为石英坩埚的内层,可有效减少内表面气泡破裂现象,为长时间拉晶(如多次复投料)提供保障。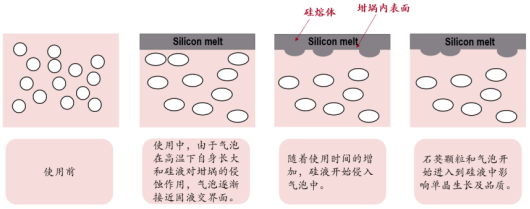
坩埚生产环节用高纯石英砂标准较光伏玻璃石英砂更严苛。光伏坩埚用石英砂纯度需达到99.998%,光伏生产环节用(如清洗环节)石英制品纯度要求为99.99%以上,均高于光伏玻璃石英砂98.55%的纯度要求。目前,石英坩埚内涂层对高纯石英砂纯度要求更高,纯度等级需要达到4N8(SiO2=99.998%),而石英坩埚外涂层、石英管、石英棒、石英舟和石英锭等产品达到4N5即可。石英坩埚中内层对高纯石英砂高纯、低铝、低碱、抗析晶的要求更高。坩埚最内表层是指透明层中最靠近内表面1-2mm的部分。坩埚对硅液起作用的机理是,由于与硅液接触的内表面不断向硅液中熔解,并且伴随着透明层中的微气泡不断的长大,靠近最内表面的气泡破裂,伴随着硅液释放石英微颗粒以及微气泡。而这些杂质会以微颗粒以及微气泡的形式伴随着硅液流遍整个硅熔体,直接影响到硅的成晶(整棒率、成晶率、加热时间、直接加工成本等)以及单晶硅的质量(穿孔片、黑芯片等)。《重点新材料首批次应用示范指导目录(2018年版)》明确提出半导体级电弧石英坩埚,规格:14~24寸;内层纯度:所有金属杂质含量<12ppm;强度:1500度高温变形率<2%;寿命可达200小时。目前,国内适用于光伏、半导体纯度等级的高纯石英砂产能有限。石英坩埚内层砂仍以国外进口为主。而连续多次投料等拉晶发展方向对石英砂纯度提出更高要求。寻找高品质石英矿源、提升提纯技术尤为迫切。未来,随着国内在坩埚尺寸、纯度、拉晶时间和拉晶次数等方面的提升。以及国内石英坩埚具有一定的成本优势,石英坩埚国产替代将进步加速。声明:转载此文是出于传递更多信息之目的。若有来源标注错误或侵犯了您的合法权益,请作者持权属证明与本网联系,我们将及时更正、删除,谢谢。
来源:粉体网
管理员
该内容暂无评论